Understanding Injection Mold Tooling: A Comprehensive Guide for Metal Fabricators
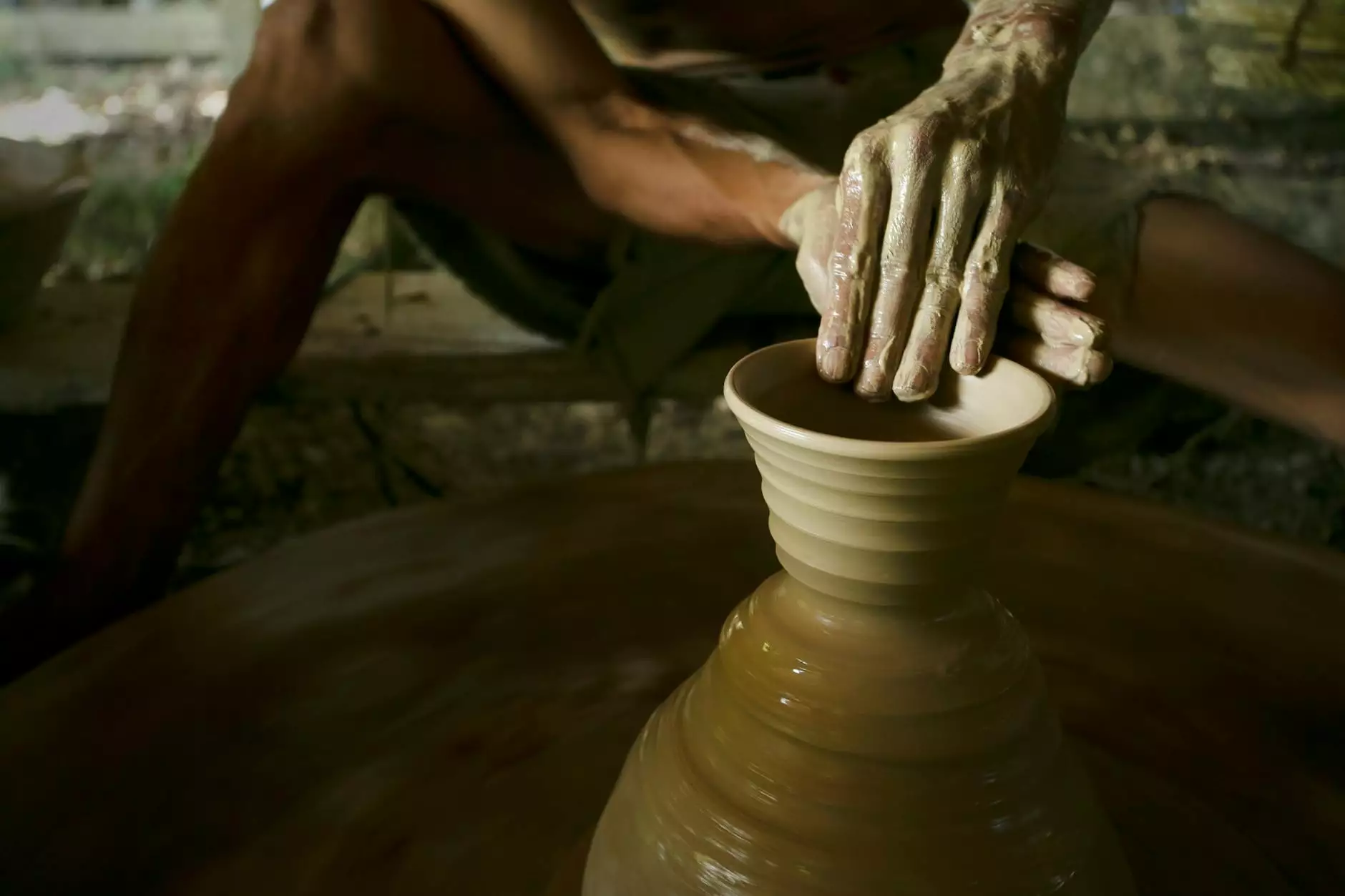
In the dynamic realm of manufacturing, injection mold tooling plays a pivotal role, especially for metal fabricators. It is an essential process that ensures the creation of precise and durable components across various industries. This article delves into the intricacies of injection mold tooling, its benefits, applications, and why it is indispensable for metal fabrication businesses like deepmould.net.
What is Injection Mold Tooling?
Injection mold tooling is a manufacturing process used to produce parts by injecting molten material into a mold. This process is prevalent in industries such as automotive, aerospace, electronics, and consumer goods. The tooling itself is a specialized setup that encompasses the mold, machinery, and various components required to deliver precise and efficient production.
Key Components of Injection Mold Tooling
The injection mold tooling system consists of several critical components:
- Mold Base: The foundation that supports the mold cavities.
- Mold Cavity: The part of the mold that shapes the molten material into the desired form.
- Injection Unit: The machinery that melts and injects the material.
- Cooling System: An integral part that controls the temperature during the injection and solidification process.
- Ejection System: The mechanism that facilitates the removal of the molded part from the cavity after solidification.
The Injection Molding Process
Injection molding involves several stages that ensure high-quality production:
1. Material Selection
The first step is selecting the appropriate material, such as thermoplastics, thermosets, or metal alloys, depending on the part's required properties and applications.
2. Mold Design
A well-designed mold is crucial for effective dimensional accuracy. Design considerations include parting lines, draft angles, and surface finish.
3. Melting and Injection
In this stage, the raw material is heated until it becomes molten and is then injected into the mold cavity under high pressure.
4. Cooling and Solidification
Once injected, the material cools and solidifies, taking the shape of the mold cavity. Cooling time is a critical factor that affects cycle time and production efficiency.
5. Ejection
Finally, the mold opens, and the solidified part is ejected from the mold cavity using the ejection system.
Benefits of Injection Mold Tooling
Injection mold tooling offers numerous advantages that make it a preferred choice for many manufacturers:
- High Efficiency: The process allows for rapid production cycles, making it ideal for mass production.
- Precision and Accuracy: Injection molding achieves tight tolerances, which is vital for components that require strict dimensional specifications.
- Material Versatility: Various materials can be used, including metals, plastics, and composites, providing flexibility in manufacturing.
- Cost-Effectiveness: While initial tooling costs can be high, the cumulative cost per part decreases significantly with large production runs.
- Reduced Waste: The process minimizes material wastage, making it environmentally friendly.
Applications of Injection Mold Tooling in Metal Fabrication
Injection mold tooling is extensively used in various applications across several industries. Here are a few notable examples:
Automotive Industry
Automakers utilize injection molded components for manufacturing parts like dashboards, door panels, and brackets due to their durability and lightweight properties.
Aerospace
In aerospace, precision-engineered parts are critical. Injection molding meets these demands, producing components that withstand high stress and extreme conditions.
Consumer Electronics
From smartphone casings to internal fittings, the consumer electronics industry relies on injection mold tooling for both aesthetic and functional components.
Medical Devices
Medical devices, requiring stringent quality and regulatory compliance, benefit significantly from the precision offered by injection mold tooling.
Choosing the Right Injection Mold Tooling Provider
Selecting an injection mold tooling provider is a crucial decision for any metal fabrication business. Here are key factors to consider:
1. Experience and Expertise
Look for a provider with extensive experience in the industry. A knowledgeable team can offer better design insights and troubleshooting.
2. Quality Assurance
Ensure that the provider follows strict quality control measures. Certifications such as ISO 9001 can indicate reliability and commitment to quality.
3. Technological Capability
Advanced machinery and technology can significantly enhance production efficiency and product quality. Invest in a partner who utilizes state-of-the-art tools.
4. Customization Options
The ability to offer customized solutions tailored to specific needs is essential. A flexible provider can adapt to changing design requirements.
5. Core Values and Customer Support
A provider who values customer feedback and support can foster a strong working relationship and ensure long-term satisfaction.
Conclusion: The Future of Injection Mold Tooling in Metal Fabrication
As industries continue to evolve, injection mold tooling remains a cornerstone of metal fabrication. It not only contributes to efficiency but also enhances innovation and creativity in product design. Companies like deepmould.net serve as valuable partners in this process, offering high-quality tooling solutions designed to meet the ever-changing demands of the market. By leveraging the advances in this field, businesses can position themselves for success in an increasingly competitive environment.
Investing in advanced injection mold tooling is not merely adopting a process—it is embracing a future filled with possibilities and enhanced productivity. Embrace the transformations in manufacturing, and see how your business can thrive with state-of-the-art injection mold tooling.