The Importance of Lathing Parts in Metal Fabrication
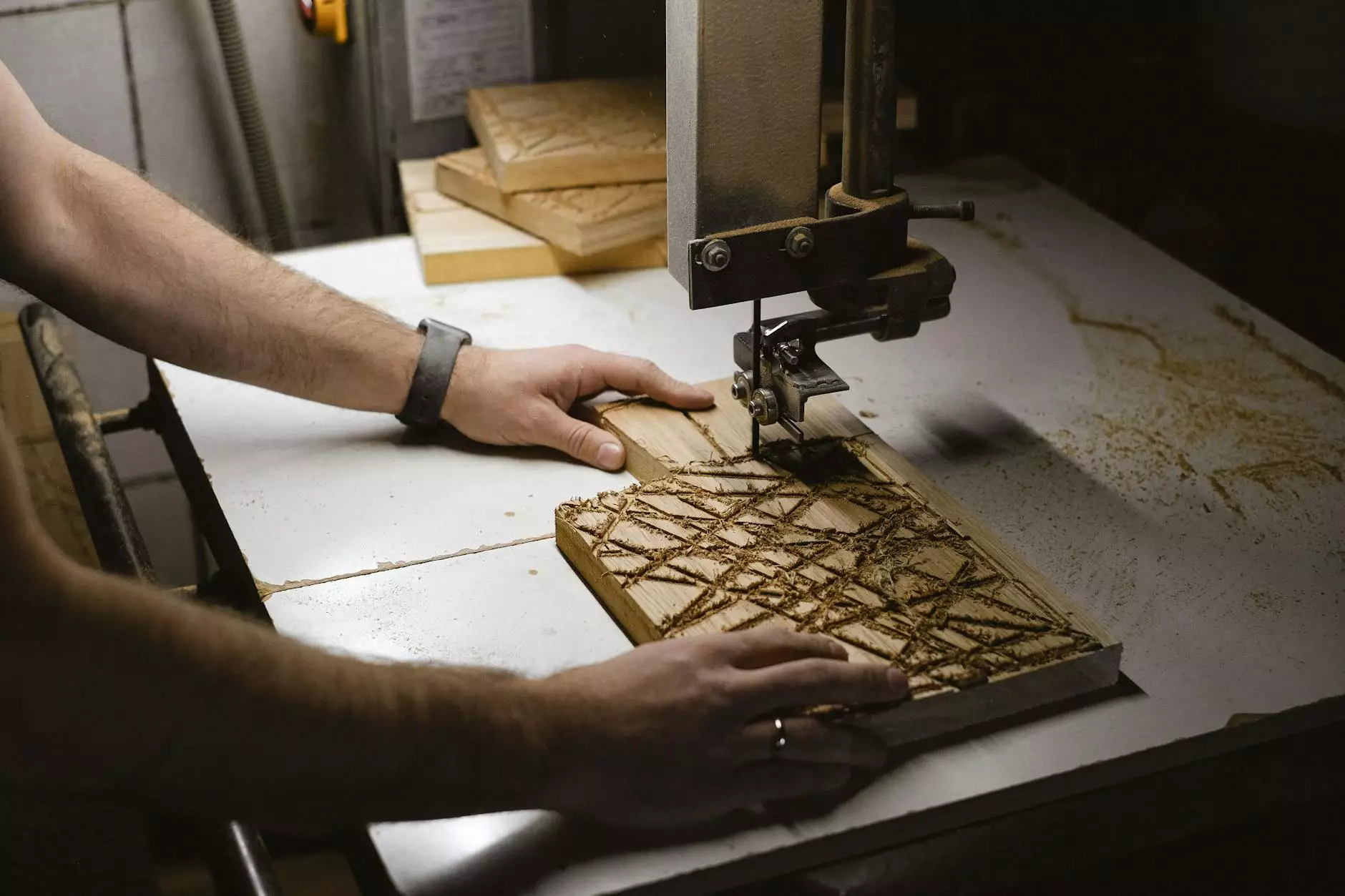
In the realm of manufacturing, precision and functionality are paramount. Among the various methods employed within the metal fabrication industry, lathing stands out as a crucial process, particularly when it comes to the production of high-quality components known as lathing parts. These components are essential in countless applications, rendering them indispensable in contemporary manufacturing practices.
Understanding Lathing Parts
Lathing involves the rotation of a workpiece against a cutting tool to create precise shapes and contours. This process is carried out on a machine known as a lathe. The resultant lathing parts exhibit a high level of accuracy, making them suitable for both aesthetic and functional roles in various industries.
Applications of Lathing Parts
Below are some significant sectors where lathing parts play a pivotal role:
- Aerospace Industry: In aerospace, lathing components are crucial for the production of precision-engineered parts that must withstand extreme conditions.
- Automotive Sector: The automotive industry relies heavily on lathing for creating various engine components, axles, and other critical parts.
- Medical Equipment: Precision lathing parts are essential in the medical field for devices requiring meticulous engineering standards.
- Industrial Machinery: Many industrial machines incorporate lathing parts within their assembly, which contributes to the efficiency and functionality of the equipment.
Benefits of Using Lathing Parts
Utilizing lathing parts has several distinct advantages:
- High Precision: Lathing offers exceptional accuracy, which is vital for components that require tight tolerances.
- Versatility: The lathing process can accommodate a wide range of materials including metals, plastics, and composites, making it adaptable across industries.
- Cost-Effective Production: Due to the efficiency of lathes, the production of lathing parts can be very cost-effective, especially in high-volume scenarios.
- Reduced Waste: The subtractive nature of lathing ensures that minimal material is wasted during production, promoting sustainability.
DeepMould's Expertise in Lathing Parts
At DeepMould, we pride ourselves on our expertise in metal fabrication, particularly in the production of high-quality lathing parts. Our company utilizes state-of-the-art machinery and advanced techniques to ensure that every component we produce meets the highest standards of quality and precision.
Our Process
The process of creating lathing parts at DeepMould involves a series of meticulously planned steps:
- Consultation: We begin by consulting with our clients to understand their specific needs and specifications.
- Design: Our design team employs advanced CAD software to draft detailed blueprints that serve as the foundation for production.
- Machining: With our cutting-edge lathes, we shape the raw materials into precise lathing parts according to the specifications outlined in the design phase.
- Quality Control: Every component undergoes rigorous inspection to ensure it meets industry standards and client expectations.
- Delivery: We ensure timely delivery of parts, adhering to project timelines without compromising on quality.
Future Trends in Lathing Parts Production
The world of metal fabrication is evolving, and trends are continuously shaping the future of lathing parts. Here are some key trends to be aware of:
- Integration of Technology: The implementation of IoT (Internet of Things) in lathes for better process monitoring and predictive maintenance.
- Adoption of Automation: Automated lathing processes are becoming more common, improving efficiency and reducing labor costs.
- Use of New Materials: The exploration of advanced materials is paving the way for new applications of lathing parts in diverse fields.
- Custom Solutions: An increasing demand for customized lathing parts tailored to specific applications is shaping production strategies.
Challenges in Lathing Parts Production
Despite the advantages, producing lathing parts does not come without its challenges:
- Material Constraints: Certain materials may pose difficulties in lathing due to their hardness or thermal properties.
- Precision Issues: Achieving the desired level of precision can be challenging, particularly with complex geometries.
- Competition: The growing competition in the fabrication industry makes it essential to continuously innovate and improve processes.
Conclusion
In conclusion, lathing parts are integral to the metal fabrication industry, offering precision, versatility, and cost-effectiveness. Companies like DeepMould are at the forefront of innovation in this sector, employing modern techniques and technologies to deliver high-quality components that meet the diverse needs of various industries.
As we look to the future, staying informed about trends, challenges, and advancements in lathing will be critical for manufacturers striving for excellence. By investing in superior processes and materials, we can continue to push the boundaries of what is possible in metal fabrication.